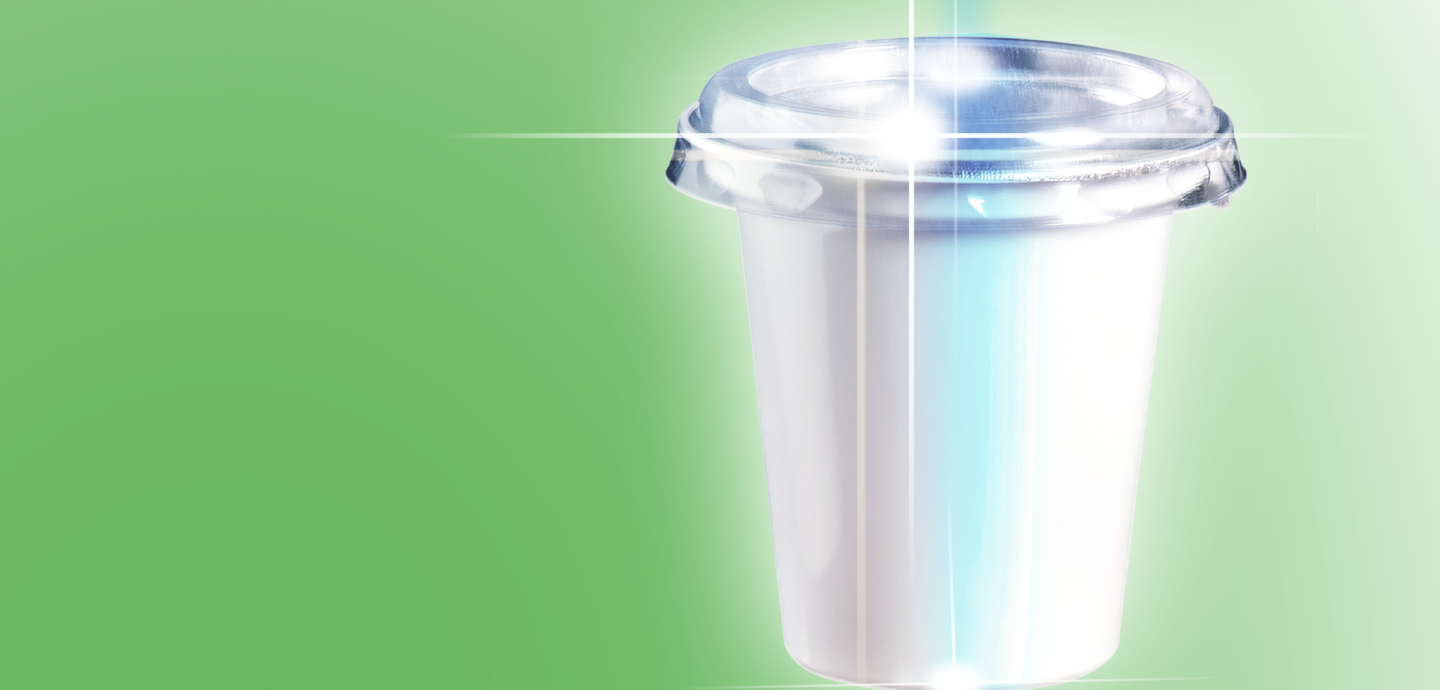
Serac makes a pulsed light decontamination solution available for cup filling lines. This technology offers an intermediate level of performance between H2O2 and UV decontamination, already part of Serac’s offering. Pulsed light enables to address new applications, such as the packaging of yogurts and desserts without additives or based on plant milks, which are growing fast.
Specifically designed for each application and extremely compact, Serac’s pulsed light decontamination modules for cups, lids and covers can be originally installed on the line or added later as part of an upgrade. Manufacturers can thus progressively adapt their production tool to market change.
Reinforced decontamination for plant-based or additive-free desserts and yogurts
The microbiological quality of core ingredients, combined with the addition of sugar and a lower acidity of the final product, make plant-based desserts and yoghurts more sensitive to the development of bacteria and molds. The same applies to the reduction or elimination of additives in milk-based yoghurts and desserts.
The conventional cleaning of cups and lids with ionized air is often insufficient to guarantee an adequate shelf life. Further decontamination is necessary to ensure sufficient reduction of the microbiological load.
Intended for health and environment sensitive targets, these products naturally call for dry, chemical-free decontamination solutions, such as UV and pulsed light.
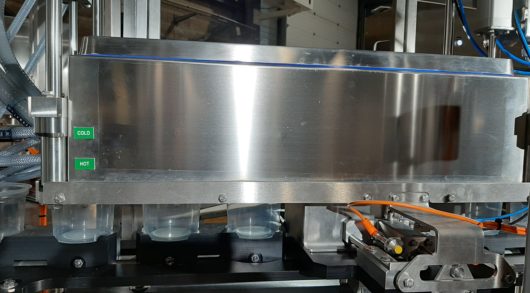
Pulsed light cup treatment on Neo machine
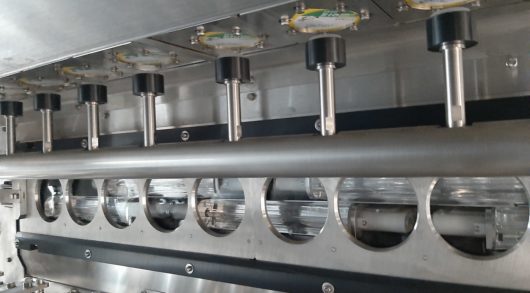
Pulsed light foil treatment on Linea machine
A chemical-free solution, efficient and fast
Pulsed light decontamination enables manufacturers to guarantee the absence of chemical residues in cups and to significantly reduce the environmental impact of their packaging process, linked to water consumption and the generation of toxic effluents.
Pulsed light exposes cups, lids and covers to very intense flashes (50,000 times the intensity of the sun’s rays on earth), which destroy the cell membrane and break the DNA chains of microorganisms. This results in a bacteriological reduction superior to that of a UV treatment, which only affects the DNA chains.
Reproducibility of the results is obtained through the customized design of the reflectors and the monitoring of the energy delivered, which ensure that light homogeneously reaches the entire surface to be treated.
Also, the exposure time required by pulsed light, less than one millisecond, is perfectly compatible with high throughput rates.
Available for rotary and linear fillers of the Serac range
Serac’s pulsed light decontamination modules can be combined with the Neo rotary fillers (with outputs from 1500 to 6000 cups/hour and 3 dosing stations) as well as with the Linea linear fillers (outputs ranging from 6000 to 40 000 cups/hour and up to 5 dosing stations working simultaneously).
They can be used to decontaminate all types of materials: PE, PS, PP, PET, PLA, cardboard, aluminum and even glass. Serac’s pulsed light offer thus covers all needs in terms of packaging materials, production volume and recipe complexity.
“ Serac offers dry and chemical-free decontamination solutions for ultra-clean packaging with pulsed light (3 log reduction) as well as for aseptic packaging with e-beam (up to 6 log reduction). The integration of pulsed light is in line with Serac's commitment to support all customers in reducing their environmental impact. “