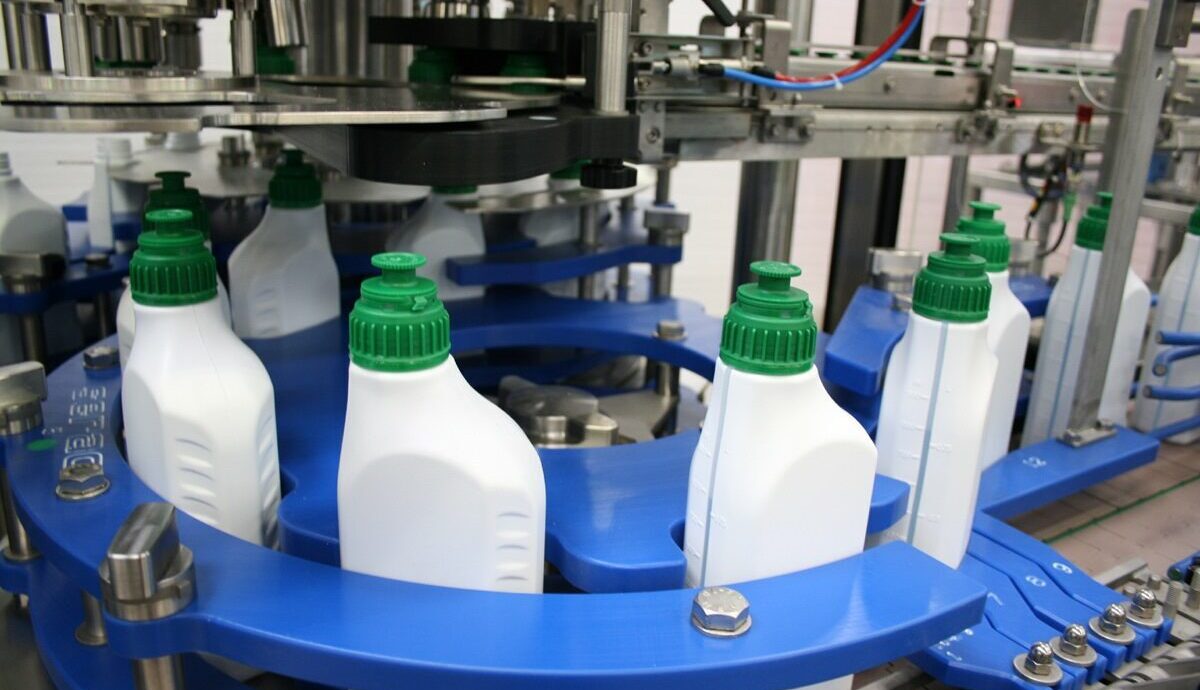
The production process of lubricating oil begins with crude oil, which undergoes sedimentation and fractional distillation to remove impurities and separate its components based on boiling points. Further refinement involves filtering, solvent extraction, and the addition of specific additives to meet desired properties. Quality control is paramount, with rigorous testing ensuring viscosity, specific gravity, color, and other crucial factors meet industry standards. Instruments like the Saybolt Universal Viscometer are utilized for viscosity measurement, while other parameters like specific gravity, color, and flash/fire points contribute to assessing quality and performance.
In automotive applications, engine oils play a vital role, classified by viscosity and performance according to industry standards established by organizations like the Society of Automotive Engineers (SAE). These specifications cover aspects such as wear prevention and deposit formation, ensuring optimal engine performance.
The importance of design and packaging for lube oil
In the mineral oil industry, the importance of design and packaging goes far beyond mere practical considerations. Beyond the functions of protection and usability, packaging plays a crucial role in attracting consumer attention.
An attractive or original packaging offers an efficient means of visual identification, establishes a trademark, and allows the product to stand out among the vast range of competitor products on the shelves. Whether made of HDPE or metal, it is essential to consider the different container requirements of their target markets.
First and foremost, functionality is a must: the container must open easily, allow for precise and efficient pouring, while ensuring adequate product protection.
The next requirement concerns ergonomics, such as user-friendliness during transport, use, and disposal. Consumers seek packaging that is easy to handle and dispose of, enhancing their overall experience.
Sustainability is also a critical aspect, with an increasing demand for environmentally friendly materials and lighter packaging, especially in the United States, Western Europe, and Australia. Consumers are increasingly sensitive to the environmental footprint of the products they purchase, and brands that address this concern gain credibility and loyalty.
Finally, anti-counterfeiting measures are becoming increasingly important on a global scale. Packaging that is difficult to replicate and equipped with security features enhances consumer confidence in the authenticity of the products they purchase.
In summary, in the competitive mineral oil market, packaging is a strategic element that goes far beyond its simple utility function. It is a powerful tool for attracting consumers, establishing a strong brand, and meeting the specific requirements of different markets worldwide. Brands that understand and invest in these aspects gain a significant competitive advantage in this constantly evolving market.
The different filling technologies
Choosing the most suitable filling technology is crucial, considering factors such as container type, product characteristics, and environmental sensitivity. Various technologies, including weight-based, constant level, volumetric, and flow metering, offer distinct advantages and limitations.
Lube oil filling traditionally relies on volume measurements, with pack sizes labeled in liters, pints, or gallons. However, weight-based filling, utilizing scales to verify correct filling, has gained prominence due to its accuracy and consistency.
Filling by weight eliminates issues related to product temperature and aeration, ensuring precise dosing consistently. Many lube oil packers now prefer net weight filling machines due to several advantages:
– High accuracy: Minimizes product loss and ensures quality filling, enhancing the image of finished products and reducing wastage.
In fact, Changes in temperature of up to 10°c could result in a volume variation.
For example, filling at 30°C with conventional technology, oil will appear at the right level of the container, but once displayed in a store at 20°c, the bottle will look underfilled. Yet, when summer comes and temperature rises to 40°C, the bottle will look overfilled.
With net weight filling, 1000 ml is always 900 grams of lubricant oils.
The use of electronic dosing modules with weight-based dosing eliminates the need for overdosing to meet minimum fill volumes, contributing to further product savings.
– Cleaner process: Non-dripping nozzles maintain cleanliness, facilitating a more hygienic packaging process.
– Material savings: Non-contact filling allows the use of lightweight containers, leading to significant packaging material savings.
– Reduced maintenance: Weight-based filling systems have fewer wear and tear parts, resulting in lower maintenance costs.
– Production reporting: Easily accessible production reports contribute to better production management and efficiency.
Overall, weight-based dosing offers unparalleled accuracy, efficiency, and cleanliness in lubricating oil packaging processes.
Various machines are available depending on the production needs
Explore Versatile Machines to Meet Your Lubricant Production Needs
When it comes to filling and capping lubricants, there’s no one-size-fits-all solution. That’s why we offer a range of machines tailored to suit various production requirements:
Semi-Automatic Filling Machine:
– Efficiency meets affordability: With a capacity of up to 700 liters per hour, this machine offers automation without breaking the bank.
– Precision at its core: Utilizing weight-based fillers, it ensures precise dosing for various oil types and packaging sizes.
Discover our semi-automatic machine
High-Speed Lubricant Filling Machines:
Unleash productivity: Rotary filling and capping machines boast impressive speeds of up to 40,000 liters per hour, perfect for high-volume production.
– Flexibility redefined: Equipped with weight-based fillers, these machines adapt seamlessly to different capacities and packaging types.
– Reliability in action: Experience minimal downtime and maximize output with low-maintenance machines boasting a remarkable 97% yield rate.
– Speed meets precision: Some models can fill and cap up to 250 containers per minute, ensuring your production line keeps pace with demand.
Whatever your lubricant production needs, our range of machines has you covered. Explore the options and take your production to the next level.
Closure Systems also depend on customer requirements. Several systems exist like electromagnetic actuators for standard manufacturing operations, pneumatic actuators for various capping operations, and electric drive for fine and complex operations requiring real-time torque control.
Serac offers the equipment and associate services to optimize the operation of production lines, from filling containers to palletizing finished products. From study to delivery, Serac leverages its experience and expertise to ensure the competitiveness of your lube oil products.
For more information about our machines and our know-how, please contact us.