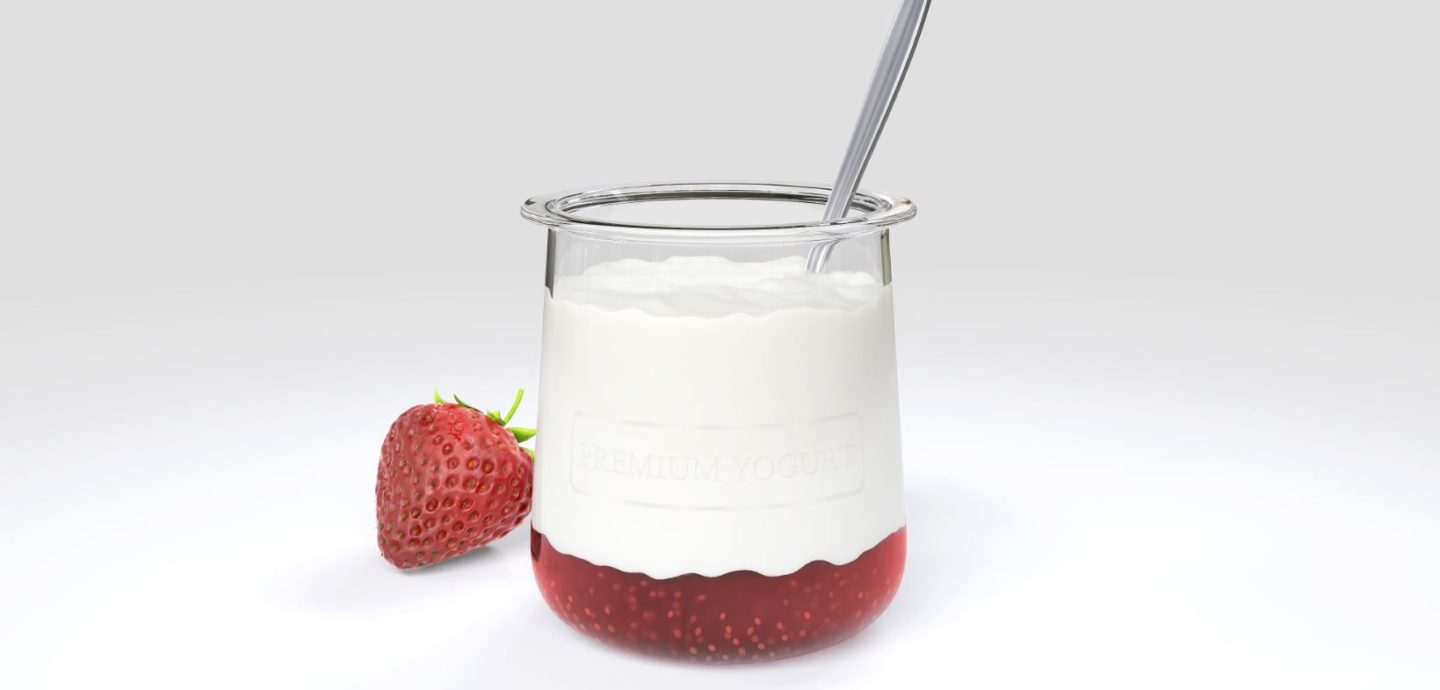
What kind of packaging should we choose to sustainably position ourselves on the market segments of premium yogurts and fresh desserts? This is the difficult question industrial manufacturers today have to answer, taking into account consumers’ expectations together with the environmental impact and the production constraints, both financial and technical, of each possible solution.
If polystyrene (PS) remains the n°1 material for standard yogurts, glass is sometimes considered as an alternative option for higher-end market segments, where cup transparency is a sales argument and targeted customers are more sensitive to environment protection.
But PET also has its own arguments.
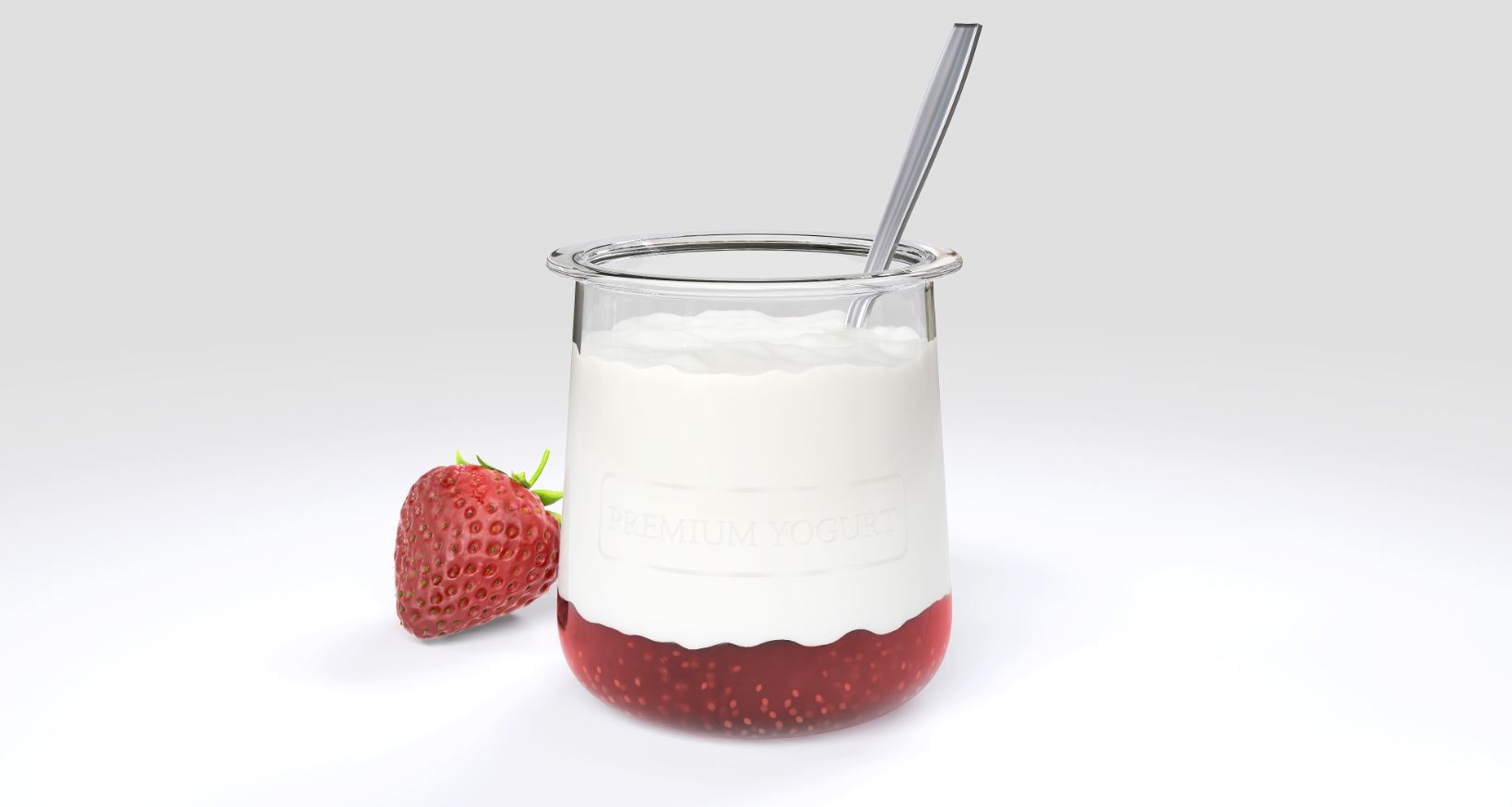
“ On the yogurts and fresh desserts markets, high-end segments are driven by 2 main trends. Naturality: high quality milk, organic fruits, no additives, no added sugar… and elaborate recipe: multi-layer products mixing tastes and textures. “
4 features of PET packaging
Transparency
On the yogurts and fresh desserts markets, transparency is a strong sales argument. It allows the consumer to see the product he is purchasing. Up to now, the high-end answer to this need was glass. But it is today possible to blow PET cups which feature the same transparency and shine as glass, whereas it is still not the case for PET and PP (polypropylene) cups thermoformed on FFS machines. The quality of blown PET is well proven for bottles : in Europe, 87,4% of water bottles are made of PET, and only 12,4% of glass*.
Why couldn’t it prove as good for cups ?
Resistance
Resistance is an argument against glass but also against transparent polystyrene. The weight/resistance ratio of PET and its shock resistance substantially contributed to its success for bottles, and allow to consider PET as an alternative to impact PS and PP.
Resistance is mainly a comfort issue for retailers as well as for consumers : it avoids breakage. But it also has an influence on a key indicator of the environmental and social performance of agrifood companies : food waste. For a broken cup is a yogurt lost.
Average weight of a glass cup versus 5 g for a PET cup
Temperature of the furnaces for producing glass. The melting temperature of PET is around 245°C.
Lightness
PET has a density of 1,3 to 1,4 against 2,5 for glass. Which means that even if glass cups could be as thin as PET ones, they would still be almost two times heavier. In practice, the gap is much more important : the weight of a plastic cup is between 4 and 5g, the one of a glass cup is 80g.
Such weight has an impact on the transportation part of the carbon footprint of a product. Bringing glass cups up to the factory, shipping them to the selling point and then collecting and transporting them to the recycling unit emits more CO2 than achieving the same cycle with a PET cup. Especially if this cup is produced within the factory.
Carbon footprint might be even more in favour of PET considering the amount of energy required for its production. It indeed has a melting point of only 245°C where glass is produced in furnaces heated at 1500°C. Regarding the dependence on fossil fuels, progress is also being made with companies such as Origin Materials, which can produce PET from cellulose.
Recyclability
Glass is, in consumers’ mind, a « good » material as far as waste management is concerned. It is known as being infinitely recyclable and its collection has been well organized for years. It can even be used in deposit systems. According to a FEVE** study, 85% of Europeans would recommend glass as a packaging material.
But on the PET side, a circular economy is emerging. PET is 100% recyclable and rPET is approved for food contact. Already used in « bottle-to-bottle » loops, it could as well be used in « cup-to-cup » loops to reach the same recycling rates as glass.
Transparency, lightness, resistancy and recyclability : 4 features which, together, make a high-quality and sustainable packaging and for which PET is very well placed.
* Source Petcore Europe/Global data
** FEVE : the European Container Glass Federation